Step-by-Step Guide to Designing and Building a Prefabricated Home
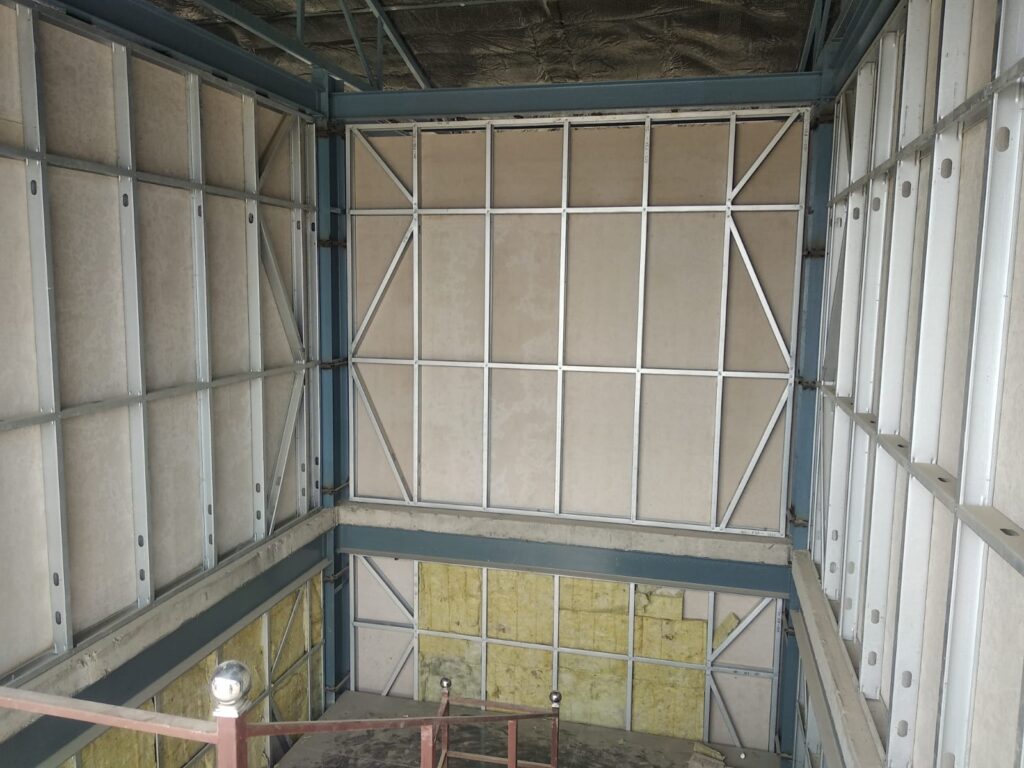
Light Gauge Steel Frame Construction Building and prefabricated home can be a streamlined and efficient process, but it requires careful planning and coordination. Here’s a step-by-step guide to help you navigate through the process of designing and building your dream prefabricated home.
1. Initial Planning and Budgeting of Light Gauge Steel Frame Construction
a. Define Your Needs and Goals
- Determine the size and type of Prefabricated home you need.
- Consider the number of rooms, layout, and any special features you desire.
b. Set a Budget
- Establish a realistic budget for your project, including land, design, construction, and any additional costs.
- Research financing options such as loans or mortgages specifically for prefabricated homes.
c. Select a Location
- Choose a suitable plot of land for your Light Gauge Steel Frame or Prefabricated home.
- Ensure the site is accessible and meets local zoning and building regulations.
2. Design and Customization
a. Choose a Prefabricated Home Manufacturer
- Research and select a reputable prefabricated home manufacturer.
- Look for manufacturers with positive reviews and a portfolio of successful projects.
b. Design Consultation
- Meet with the manufacturer’s design team to discuss your vision and requirements.
- Customize floor plans and select materials, finishes, and fixtures.
- Ensure the design meets local building codes and regulations.
c. Finalize the Design
- Review and approve the final design plans and specifications of Light Gauge Steel Frame Construction.
- Confirm the timeline and schedule for the construction process.
3. Permitting and Approvals Light Gauge Steel Frame Construction
a. Obtain Necessary Permits
- Submit the design plans to local authorities for approval.
- Secure all necessary building permits, zoning approvals, and any other required documentation.
b. Site Preparation
- Prepare the site for Light Gauge Steel Frame construction, including clearing the land and laying the foundation.
- Ensure all utility connections (water, electricity, sewage) are in place.
4. Manufacturing the Home
a. Off-Site Construction
- The prefabricated modules or panels are manufactured in the factory.
- Each module is built to the exact specifications of the design plans.
b. Quality Control
- The modules undergo rigorous quality control checks to ensure they meet all standards.
- Inspections are conducted at various stages of the manufacturing process.
5. Transportation and Assembly
a. Transporting the Modules
- The completed modules are transported from the factory to the building site.
- Ensure proper logistics and transportation permits are in place.
b. On-Site Assembly
- The modules are assembled on-site, typically using cranes to position them.
- The assembly process is quick, often taking only a few days to complete.
c. Securing and Connecting the Modules
- The modules are securely fastened together and to the foundation.
- Utilities are connected, and the home is made weather-tight.
6. Finishing Touches
a. Interior and Exterior Finishing
- Finish the interior work, including flooring, painting, and installing fixtures.
- Complete any exterior work, such as siding, roofing, and landscaping.
b. Final Inspections
- Conduct final inspections to ensure the home meets all safety and quality standards.
- Address any last-minute touch-ups or adjustments.
Conclusion
Building a Light Gauge Steel Frame Construction or prefabricated home offers a unique blend of efficiency, customization, and quality. By following these steps, you can navigate the process smoothly and create a home that meets your needs and reflects your personal style. With proper planning and the right team, your prefabricated home can be a cost-effective and sustainable solution that provides comfort and satisfaction for years to come.