A Checklist: Essential Steps for PEB Project Success
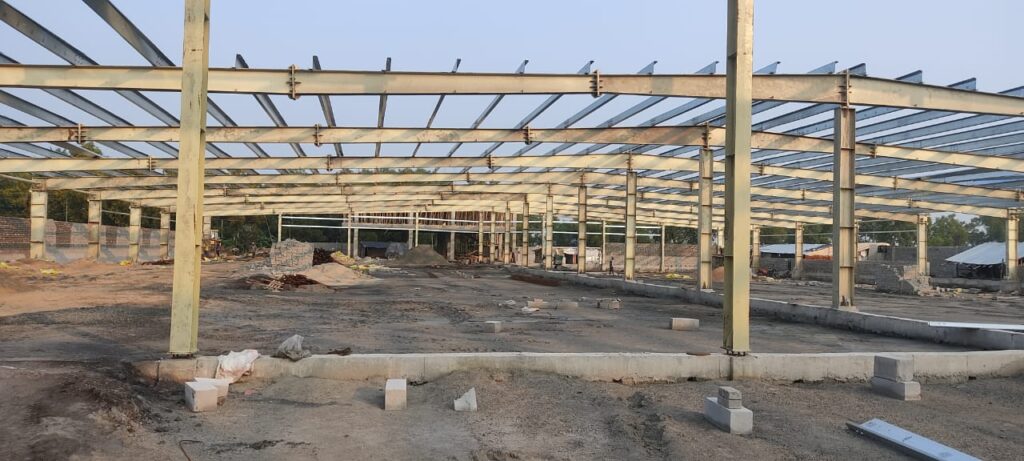
Pre-Engineered Buildings (PEBs) are transforming the construction industry by offering faster project timelines, cost efficiency, and design flexibility. However, ensuring the success of a PEB project requires careful planning and execution. Here’s a comprehensive checklist to guide you through the essential steps for a successful PEB project.
1. Define Project Objectives and Scope
Before starting, clearly outline:
- Purpose of the PEB: Is it for a warehouse, factory, commercial space, or another use?
- Key Specifications: Dimensions, load requirements, and environmental conditions.
- Budget and Timeline: Establish a realistic budget and target completion date.
2. Choose the Right Team
- Select a Reliable PEB Manufacturer: Opt for manufacturers with proven experience and quality certifications (e.g., ISO 9001).
- Engage Qualified Designers and Engineers: Collaborate with professionals familiar with PEB systems to ensure precision in design.
- Hire Experienced Contractors: Look for contractors with expertise in PEB erection and installation.
3. Conduct Site Assessment
- Perform a thorough site survey to evaluate:
- Soil conditions and load-bearing capacity.
- Accessibility for transportation and equipment.
- Climate factors like wind speed, snow load, and seismic activity.
4. Finalize the Building Design
- Work with your design team to develop a detailed plan:
- Structural Layout: Optimize for load distribution and functionality.
- Aesthetics: Incorporate architectural preferences like façade cladding and color schemes.
- Compliance: Ensure designs meet local building codes and safety regulations.
5. Material Selection
- Choose high-quality materials tailored to your project’s requirements:
- Steel Grades: Select appropriate grades for strength and durability.
- Roofing and Cladding: Opt for corrosion-resistant materials to withstand environmental conditions.
- Insulation: Use thermal and acoustic insulation if needed for energy efficiency and comfort.
6. Plan Logistics and Procurement
- Develop a logistics strategy for seamless material delivery:
- Coordinate with suppliers for on-time procurement.
- Plan for storage and handling of components at the site.
- Factor in transportation restrictions and challenges, especially for large structural parts.
7. Prepare the Foundation
- Ensure that the foundation is constructed to meet the specific requirements of your PEB structure.
- Verify alignment, leveling, and dimensions for accurate assembly of components.
8. Erection and Assembly
- Use skilled labor and advanced tools for assembly:
- Follow the manufacturer’s guidelines for step-by-step erection.
- Ensure proper bolt tightening and welding for stability.
- Conduct regular quality checks during this phase to avoid alignment or structural issues.
9. Perform Quality Inspections
- Check all structural connections, including joints, bolts, and welds.
- Inspect roofing and cladding for proper installation and sealing.
- Conduct load testing where required to confirm structural integrity.
10. Ensure Safety Compliance
- Implement strict safety measures for workers on-site, such as using helmets, harnesses, and other protective equipment.
- Ensure compliance with OSHA or local safety standards to avoid legal complications.
11. Plan Utilities and Interior Fit-Outs
- Coordinate the installation of utilities such as electrical systems, HVAC, plumbing, and fire safety systems.
- Customize interiors based on the building’s purpose, including partitions, flooring, and lighting.
12. Final Handover and Maintenance Plan
- Conduct a walkthrough with the client to review the finished project.
- Provide a detailed maintenance manual for the structure, including periodic inspection schedules and care instructions.
Bonus Tips for Success
- Communicate Regularly: Maintain open communication with all stakeholders to address issues promptly.
- Leverage Technology: Use tools like Building Information Modeling (BIM) to visualize and plan your PEB project more effectively.
- Focus on Sustainability: Opt for eco-friendly materials and designs to enhance energy efficiency.
By following this checklist, you can ensure a smooth and successful Pre-Engineered Building project, delivering value and performance to your clients.